Fonte e Fotos: Universidade Federal de Santa Catarina - 01/11/07
Histórico da Furação por Escoamento
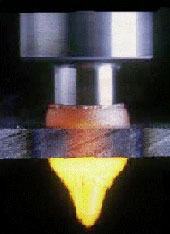
A primeira tentativa de produzir furos em chapas finas de aço sem a retirada de cavacos, aproveitando-se do calor gerado pelo contato com a peça de uma ferramenta giratória, foi realizada em 1923 pelo francês Claude de Valliere. Em função da falta de um material mais adequado para a ferramenta, como por exemplo o metal duro - que foi introduzido na fabricação somente em 1927 - esta apresentava uma vida extremamente baixa.
Na época, além de não se dispor da tecnologia de fabricação da ferramenta não se conhecia exatamente a sua geometria. Nos anos 20 este processo também era conhecido nos EUA, entretanto não existem registros sobre aplicações. Mais tarde, em 1957, outro francês, Armand Leroy, registrou uma patente com o título "Processo e ferramentas para a fabricação de buchas e as buchas resultantes deste processo", sem entretanto mencionar aplicações práticas.
Na década de 60 foi apresentada a primeira aplicação industrial da furação por escoamento de que se tem notícia, desenvolvida pelo holandês J. van Geffen, que denominou o processo de vloei-borens. De 1972 a 1977 van Geffen desenvolveu outros tipos de ferramentas que obtiveram sucesso em aplicações práticas. A partir destas ferramentas foram registradas várias patentes holandesas até o final da década de 70.
Nessa época surgiram outros casos de aplicação na Holanda e na Inglaterra. A partir do início da década de 70 iniciaram-se as primeiras pesquisas acadêmicas sobre furação por escoamento na Universidade de Siegen, Alemanha, no sentido de encontrar fundamentos tecnológicos para a aplicação do processo em outros materiais.
Em 1980 o prof. Kretschmer, desta mesma universidade, defendeu a tese de doutorado com o título "Furação por escoamento". Na década de 80 as linhas de pesquisa se difundiram para outras instituições, como a Universidade Tecnológica de Twente, Holanda, sob a orientação do Prof. H. J. J. Kals, na Universidade Integrada de Kassel, Alemanha, sob a orientação do Prof. Franz Tikal, e também pela empresa British Steel Tubes and Pipes.
No Brasil, pesquisas nesta área foram iniciadas em 1991 no Laboratório de Mecânica de Precisão (LMP) do Departamento de Engenharia Mecânica da Universidade Federal de Santa Catarina sob orientação do Prof. Walter L. Weingaertner em convênio com a empresa Flowdrill B.V.
O Princípio da Furação por Escoamento
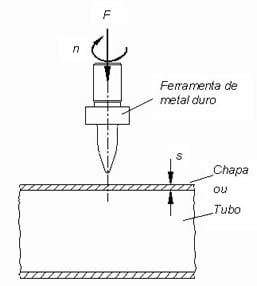
Segundo a norma VDI 3359, de 1986, o processo de furação por escoamento é aquele em que uma ferramenta cilíndrica, de metal duro e de ponta cônica, é rotacionada e pressionada com uma força F contra a peça, como mostrado na figura ao lado.
Através da rotação n, é gerado atrito entre a ferramenta e a peça, que produz o calor necessário para diminuir a resistência do material e aumentar a sua plasticidade, facilitando a sua conformação.
Estudos mais recentes citam que a maior parcela de geração de calor se deve às deformações localizadas, promovidas pela passagem dos lóbulos da ferramenta, quando em contato com a peça, e não ao atrito dinâmico entre as superfícies da ferramenta e da peça. Estes fatores combinados geram o calor necessário para aumentar a plasticidade do material, escoando-o nas direções axial e radial, sendo então conformado numa bucha.
König define os processos de furação como aqueles que possuem um movimento rotativo principal, onde a ferramenta apresenta apenas um movimento de avanço, na direção do eixo de rotação. Deste modo, a furação por escoamento pode ser classificada como um processo de furação. Entretanto, por não haver remoção de cavacos não pode ser considerado como um processo de usinagem, e sim um processo de conformação.
Ferramentas Utilizadas no processo
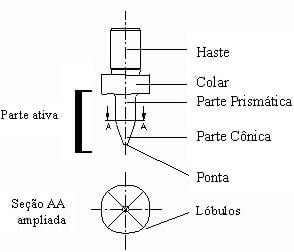
A furação por escoamento emprega ferramentas de geometrias especiais para a produção da bucha sem remoção de material. A figura ao lado mostra a geometria da ferramenta, com a parte ativa de seção cônica-poligonal em destaque.
Esta geometria composta de lóbulos, salientes na superfície da ferramenta, promove deformações localizadas no material, o qual aumenta de temperatura e reduz o limite de escoamento. Com o material da peça neste estado é realizada a conformação da bucha, sem remoção de cavacos.
A Sequência de Operação
A seqüência de conformação da bucha é ilustrada na figura abaixo, onde se percebe o escoamento do material no sentido superior e inferior da chapa. Durante a fabricação da bucha a conformaçãabo do material da peça ocorre a diferentes taxas de deformação, diferentes temperaturas e plasticidades existentes na região de trabalho. Na entrada da ferramenta a ponta cônica desenvolve um processo de deformação à frio quando o material começa a escoar para cima da chapa. A medida que a ferramenta penetra na peça a temperatura aumenta, diminuindo a resistência do material e facilitando a sua conformação.
Equipamentos Utilizados
Na furação por escoamento podem ser utilizadas as mesmas máquinas-ferramentas empregadas em outros processos de furação. Entretanto, na seleção da furadeira deve-se garantir rigidez e potência de acionamento suficientes, bem como uma faixa de rotações disponíveis adequada.
O uso de máquinas CNC é recomendado, pelas características acima e também pela possibilidade de programação da rotação e da velocidade de avanço de forma variável em processo, permitindo uma otimização dos resultados de trabalho e do tempo de processo. Em relação à peça devem ser levados em consideração o seu material, a geometria, as suas respectivas propriedades termofísicas/mecânicas e também a distância entre os furos.
A espessura mínima da peça necessária à produção da bucha situa-se na faixa de 1,5 a 2,0 mm, quando ferramentas para M6 e M8 podem ser utilizadas. Como limite superior tem-se o valor de 16,0 mm de espessura, em ferramentas com diâmetro > 20 mm.
Aplicações da Furação por Escoamento
A seguir são apresentados alguns tipos de uniões e fixações removíveis utilizadas em chapas finas ou peças de pequena espessura, onde a furação por escoamento encontra aplicação. Entende-se como removível a fixação que pode ser desmontada sem que as peças que a compõem sejam inutilizadas. As soluções convencionais para a fixação de peças de pequena espessura normalmente requerem várias etapas de fabricação, além do uso de máquinas-ferramentas especiais, que tornam a sua produção complexa. Alguns problemas comuns destas soluções incluem a capacidade de vedação insuficiente, quando tais sistemas são aplicados em vasos de pressão e a quebra devido à fadiga, na presença de solicitações dinâmicas. Além disso, na maioria dos casos, há remoção de material e adição de elementos externos na peça.
A produção de uniões em chapas finas, como ilustrado na figura abaixo, requer quase sempre a utilização de elementos adicionais, como rebites e porcas, ou a utilização do puncionamento, a fim de aumentar a área roscada disponível para uma fixação. Isto é necessário em uniões onde o comprimento roscado disponível é geralmente de resistência insuficiente às cargas em trabalho. Buchas roscadas podem ser aplicadas na maioria dos casos, com vantagens, em substituição às soluções convencionais. Entretanto, a viabilidade econômica desta substituição deve ser analisada caso a caso.
Em estruturas metálicas (construção civil) geralmente são utilizadas fixações roscadas de grandes diâmetros em chapas mais espessas, em função de solicitações mais críticas em trabalho. Embora a utilização da furação por escoamento neste tipo de aplicação ainda não tenha sido largamente difundida, estudos mais recentes demonstram que buchas roscadas são capazes de suportar elevadas cargas de tração e de cisalhamento, sendo, portanto, adequadas ao uso em estruturas metálicas.
Buchas roscadas também encontram aplicações com êxito em sistemas submetidos a altas pressões de trabalho, como a da figura abaixo, os quais muitas vezes são submetidos a solicitações dinâmicas. Em tubulações fechadas o uso desta tecnologia permite a produção de fixações sem a necessidade de acesso ao interior do tubo. Nesta situação a não-produção de cavacos se apresenta como uma vantagem decisiva.
Considerações Finais
Em função dos resultados obtidos neste trabalho, uma análise econômica do emprego de condições de trabalho variáveis em processo na furação por escoamento revela as suas principais vantagens:
- Diminuição drástica do tempo principal do processo;
- Melhoria na capacidade de carga das buchas roscadas;
- Potência de acionamento requerida em patamares usuais.
Entretanto, a utilização da tecnologia da furação por escoamento ainda está em processo de amadurecimento na indústria. Em função disso, e apesar de vários trabalhos nesta área já terem sido realizados, o domínio do emprego desta tecnologia em máquinas CNC ainda está longe de ser alcançado.
Referências Bibliográficas
Este trabalho foi extraído da dissertação de mestrado do aluno: Otacílio Cardoso Duarte Filho defendida em fevereiro de 1998, no Departamento de Engenharia Mecânica da Universidade Federal de Santa Catarina e dos seguintes trabalhos:
1. OLIVEIRA, C. A. S.; WEINGAERTNER, W. L.; ECKHARDT, M. e DUARTE FILHO, O. C.; Efeito das Condições de Trabalho da Furação por Escoamento sobre as Características de Processo e Microestrutura de Buchas Escoadas; 53 Congresso Anual da ABM, Belo Horizonte /setembro, 1998, publicado em CD-ROM;
2. OLIVEIRA, C. A. S., WEINGAERTNER, W. L.; ECKHARDT, M. e DUARTE FILHO, O. C.; Efeito das Condições de Trabalho da Furação por Escoamento sobre as Características das Buchas Escoadas e nas Propriedades de Buchas Roscadas; Anais da I Conferência Nacional de Conformação de Chapas, eds. Lirio Schaeffer, Porto Alegre, RS, outubro / 1998; pp. 101 -114;
3. OLIVEIRA, C. A. S.; WEINGAERTNER, W. L.; ECKHARDT, M. e DUARTE FILHO, O. C.; Efeito do Processo de Furação por Escoamento na Microestrutura de Buchas Escoadas; 13 Congresso Brasileiro de Engenharia e Ciência dos Materiais, Curitiba /dezembro, 1998, publicado em CD-ROM.
Colaboração
Prof. Carlos Augusto Silva de Oliveira: Professor da Área de Conformação da UFSC.