O IPT está desenvolvendo no Parque Tecnológico de São José dos Campos projeto de instalação do Laboratório de Estruturas Leves (LEL), que permitirá aos seus pesquisadores trabalhar com materiais compósitos e metálicos leves, em processos inovadores de fabricação, apoiando diferentes segmentos da indústria, como os de aeronáutica, energia e automotivo, entre outros.
Em 2012, foram deflagradas várias ações para viabilizar o laboratório, garantindo assim a continuidade desse projeto originalmente lançado em 2009, com apoio financeiro do Governo do Estado de São Paulo. O investimento total é de R$ 44,2 milhões, viabilizados também com financiamento de R$ 27,6 milhões do Banco Nacional de Desenvolvimento Econômico e Social (BNDES) e mais recursos do próprio IPT, do município de São José dos Campos, da Secretaria de Desenvolvimento Econômico, Ciência e Tecnologia, mais Fapesp e Finep.
Em setembro de 2012, foi realizada visita à planta industrial do fabricante MAG / Cincinnati, sediada em Hebron, Kentucky (Estados Unidos), para a inspeção e acompanhamento dos testes de recebimento da máquina de deposição de fitas Automatic Tape Layer, adquirida pela Fapesp com recursos do BNDES.
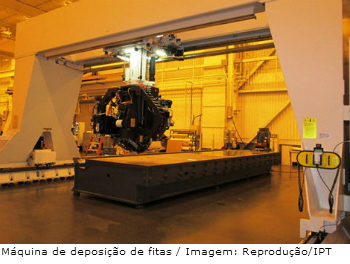
Esse equipamento realiza o processo de fabricação de peças com superfícies côncavas ou convexas de grandes raios de curvatura, utilizando materiais compósitos avançados, sólidos ou estruturados. As peças podem ter dimensões de até 4,0 m de largura e 12,0 m de comprimento. A máquina consiste em um pórtico de aço, com movimento longitudinal sobre guias de apoio, que suporta um carro com deslocamento transversal e ainda um conjunto com movimento vertical, onde fica o cabeçote de deposição de fita, montado em eixo rotativo.
O equipamento foi embarcado nos Estados Unidos e chegou ao LEL, em São José dos Campos, em novembro de 2012. O equipamento passou então para a fase de instalação, com previsão para ser comissionado em maio de 2013.
Também em 2012 foi concluído o projeto executivo da reforma de adequação do pavilhão que abrigará o laboratório, incluindo a construção da sala limpa, com 1.600 m2, controle de temperatura, umidade e partículas (Classe 9 da ISO 14.644). Essas obras estão em fase final de contratação, com previsão para início em abril de 2013. A previsão para a conclusão das obras e instalação do laboratório é dezembro de 2013.
Outros equipamentos que farão parte do LEL também foram licitados e adquiridos em 2012 pelo IPT, com os recursos do BNDES. Entre eles, destacam-se:
Máquina de solda por atrito (Friction Stir Welding - FSW): Esse processo consiste na solda em estado sólido, em que uma ferramenta cilíndrica em rotação penetra na linha de junção entre duas partes de chapa ou placa. O calor gerado pelo atrito amolece o material, sem atingir o ponto de fusão, que também é plastificado e forjado pelo contato íntimo com a ferramenta. O fornecedor do equipamento é a empresa MTI - Manufaturing Technology Inc., de South Bend, Indiana, nos Estados Unidos. A entrega final do equipamento, instalado no LEL, está prevista para Julho de 2013.
Sistema automático para conformação superplástica: É constituído por um atuador hidráulico e um quadro de reação equipado com um forno, circuito pneumático e sistema de controle. Tem por finalidades conformar chapas de metal na condição superplástica em matrizes com gás pressurizado; soldar por difusão duas ou mais chapas, aplicando forças em temperaturas adequadas; e conformar chapas metálicas a quente pela aplicação de forças controladas. O fornecedor do equipamento é a empresa Accudyne Engineering and Equipment Company, sediada em Bell Gardens, Califórnia, nos Estados Unidos. A previsão de instalação no LEL e entrega final do equipamento é novembro de 2013.
Sistema de Autoclaves: É constituído por duas autoclaves e equipamentos periféricos adequados para a cura de peças em material compósito de matriz polimérica e para conformação de chapas de ligas metálicas por processos como creep age forming. As autoclaves são vasos de pressão cilíndricos horizontais com dimensões úteis de 1 m de diâmetro por 1,5 m de comprimento e 1,5 m de diâmetro por 4,5 m de comprimento; as temperaturas máximas de trabalho são de 450°C e 250°C respectivamente. Os equipamentos possuem sistemas de controle de pressão e temperatura, sistemas de vácuo e de processamento de água de resfriamento. O fabricante do equipamento é a empresa brasileira Ferlex Autoclaves. Em setembro, houve a entrega técnica no fabricante e, em novembro, foi finalizada a instalação no laboratório. Os testes finais, na potência máxima, serão realizados assim que a reforma da subestação elétrica que alimentará o laboratório estiver concluída.